2. Equipment Selection and Specifications
This section contains the criteria used for selecting our solar panel module, inverter, and battery units. A separate section lays out the battery selection for the Animal Science Complex, as the use case profile emphasizes the importance of the research and equipment housed in this building.
​
2.1. SOLAR MODULE SELECTION
​
We analyzed 22 different modules, all above 385 W power ratings, before making our selection. Using various specifications as shown in Table 2.1 below, along with cost analysis, we selected the Jinko Solar JKM540M-7TL40-V to use in each of our designs.

Based on the guidance from our mentor at 127 Energy, we aimed to increase our energy offset using larger, more powerful modules. The JKM540 was both the most powerful and efficient module we considered, and although it is the heaviest, we chose to focus on maximizing energy savings rather than minimizing installation cost due to the fixed construction cost assumption of $1.26/W. The emphasis on efficiency is evident in the group-designated metric (power times efficiency squared divided by weight), in which the JKM540 performed the best. In addition, and perhaps most importantly, JKM is a highly trusted supplier listed as a Tier-1 solar company by Solar Review [4] and provides a 25-year linear power output warranty on a panel that is highly rated [5].
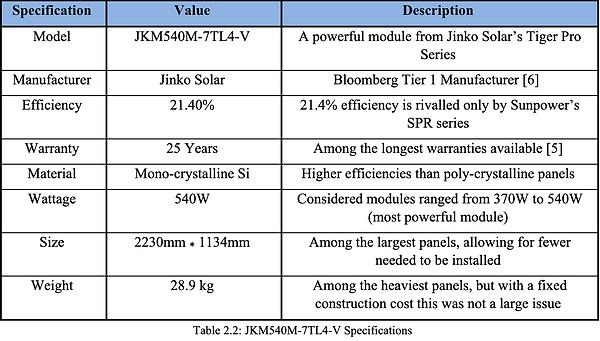
2.2. INVERTER SELECTION
​
For the selection of our inverters, we placed an emphasis on reliability and efficiency. For our initial selection of candidates, we researched the leading inverter options on the market [7]. After many design iterations, we found the best candidate to be the 33kW edition of SMA’s Sunny Tripower CORE1 series. Not only is SMA known for outstanding quality, but we found that it offered excellent pricing, high efficiency, and a solid warranty that suited our design needs [8].

2.3. EAST CAMPUS AND AGRICULTURAL FIELD MOUNTING HARDWARE
​
We chose to base our mounting hardware selection process on ease of installation, strength and stability, warranty, and industry trust. The following table outlines the features of our selected mounting hardware for the rooftop and ground-mount systems.
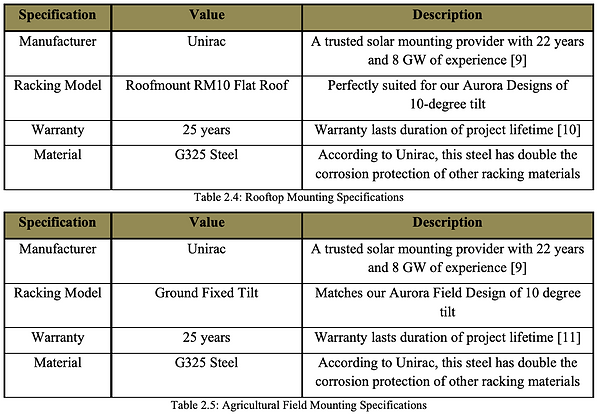
2.4. EAST CAMPUS BATTERY SELECTION
​
Based on the updated final use-case profile, which calls for strict attention to the Animal Science
Complex, we chose to implement a two-battery system to enable separate resiliency profiles for the
Animal Science Complex and the rest of the East Campus as a whole. A larger battery (1,000 kWh)
was selected for the rest of the East Campus to accommodate a larger load, shown in the table below.
We decided on this size after looking at many design iterations changing the size to see how the closely the demand charge offset was related. We plotted our results in Figure 2.1 below.
With input and help from our mentor, we modeled our battery system in Energy Toolbase. This online
solar planning tool allowed us to calculate an approximate current electric bill for UNL and an updated bill after implementing our solar + storage system. In our mentor’s words, “battery sizing is more of an art than a science.” With our quoted cost per kWh for the battery ($/kWh) in Table 2.6 and Figure 2.1, we made the decision to size our battery system at 1000 kWh. Finding the balance between system cost and demand charge offset allowed us to achieve our hurdle rate IRR and still greatly reduce the demand charges UNL pays each month – one of our main design specifications.
​
​

Looking at Figure 2.1, we can see the diminishing returns from increasing the battery system size. With
our battery cost at $350/kWh, each capacity increase by 100 kWh costs $35,000.
2.5. ANIMAL SCIENCE COMPLEX BATTERY SELECTION
​
For the Animal Science Complex (ASC), the focus of our battery selection was geared towards the
updated battery storage challenge. With important research consisting of 30% of the Animal
Science Complex consumption, we wanted to design a system that would support these essential loads and not compromise our IRR hurdle rate. Based on a model developed by our project mentor at 127 Energy, we can predict that the 500 kWh battery system for ASC can provide power during an outage for the critical load for up to 2 hours. We also used that outage duration in a REopt Lite simulation to check the system sizing and resiliency. Figure 2.2 is a screenshot from the 127 Energy Model where the highlighted numbers represent the energy dispatch to the building. And Figure 2.3 was taken from our REopt Lite simulation report.
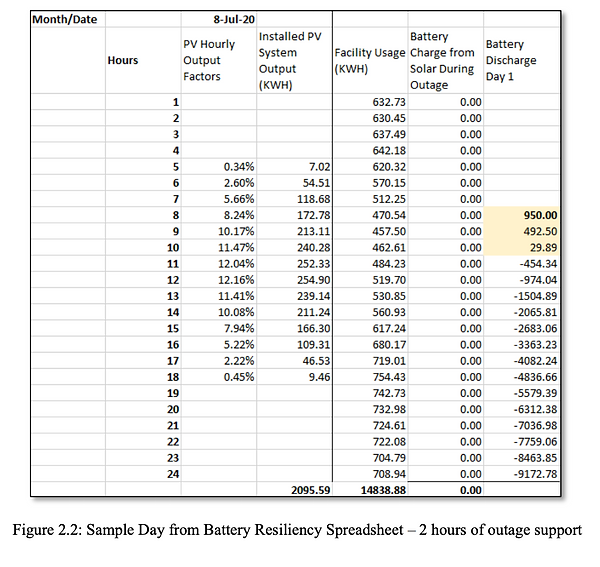

​